Revolutionising the milling of roots-type blowers: A brand new technology from Holroyd Precision
Posted by on 31 May 2017
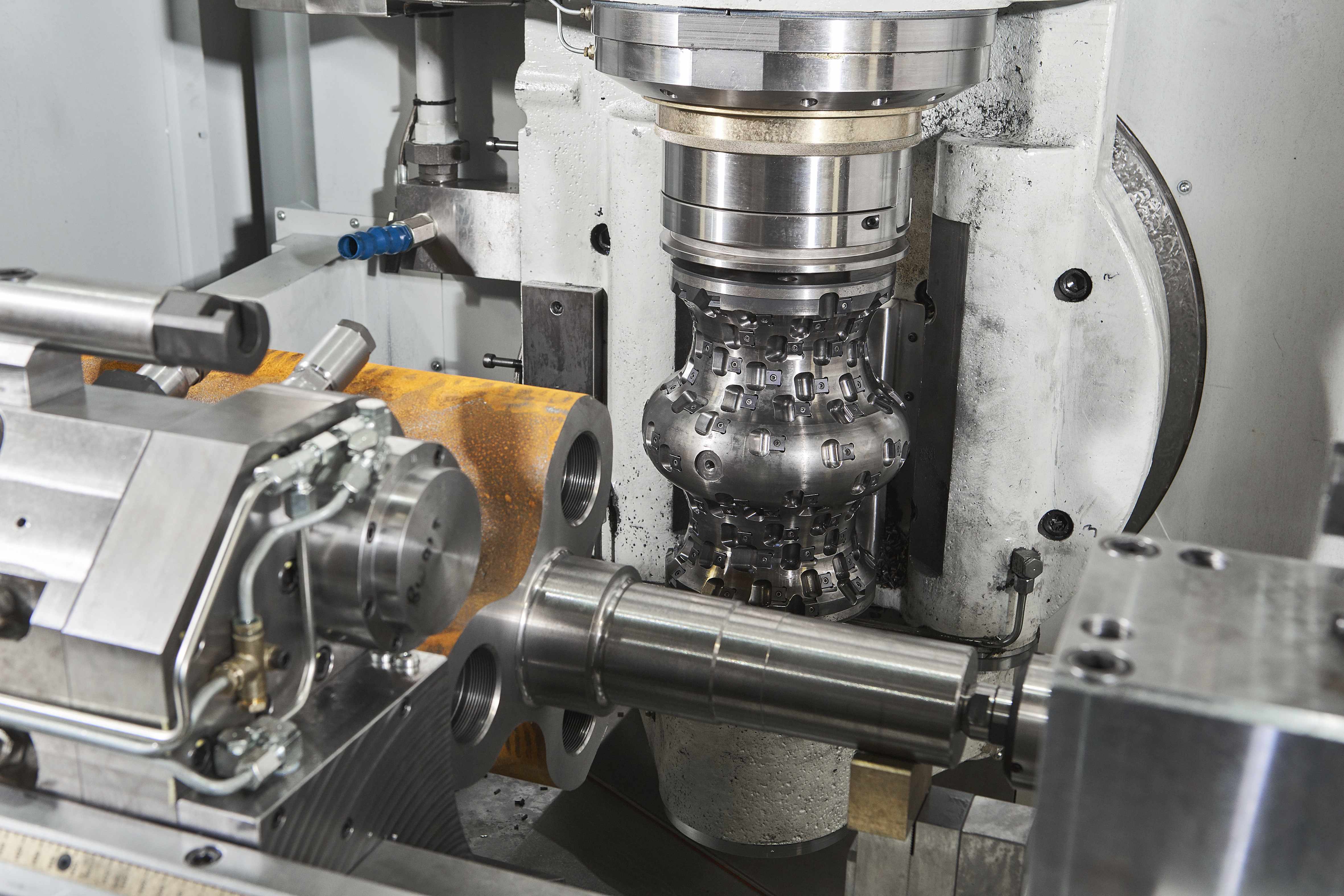
Precision Technologies Group company, Holroyd Precision, has developed a revolutionary new CNC profile milling machine that, in addition to producing helical rotors, can be programmed to precision mill straight fluted components as used in Roots-type blower ‘air ends’.
Designated as the Holroyd 4EX-R-BL (BL = blower), this latest model from Holroyd Precision brings exceptional levels of speed to the manufacture of rotors used in Roots-type blowers (also known as rotary lobe blowers). The machine is expected to be of considerable interest to blower manufacturers who wish to achieve high levels of efficiency.
Transforming the manufacture of straight-fluted rotors
“For some time we have been looking at how we can further extend the capabilities of our EX Series milling machines, to enable their high speed, high precision and high performance to be applied to the manufacture of Roots-type blowers,” comments Holroyd sales manager, Mark Curran. “We believe our new model will revolutionise the way in which straight fluted, infinitive lead rotors are milled, significantly reducing manufacturing time and increasing the accuracy of the production process.”
30-minute milling time, floor-to-floor
Although sitting within Holroyd’s EX range of rotor milling machines, the 4EX-R-BL is in fact a totally new machine that has been designed from the ground up. As well as being equipped to mill helical rotors of up to 450mm in diameter, the 4EX-R-BL will rough mill blower blanks of around 320mm in diameter and 900mm body length into straight fluted rotors in 30 minutes floor-to-floor, ready for finish profile milling to absolute size. This represents a significant time saving when compared to the one-and-a-half to two hours typically required to cut individual Roots-type blower rotor flutes using traditional milling techniques.
A bespoke solution
“Until now, manufacturers producing rotors for Roots-type blowers have been forced to either rely on NC flat bed milling machines or machining centres that have been retrofitted to absorb the considerable vibrations that occur during the flute milling process,” continues Mark Curran. “Consider the fact that when using either one of these methods each flute has to be milled in a separate operation, and it’s not surprising that the machining process for Roots-type rotors has always been labour intensive and costly.
“By contrast, the technology offered by the 4EX-R-BL moves the manufacture of Roots-type rotors away from traditional flat bed milling, where the component would be manually turned after each flute was cut, to a fully automated, programmable process able to machine both two- and three-flute blowers in one sequence.”
No manual intervention
Totally removing the need for manual intervention or indexing during the milling of each flute, the Holroyd 4EX-R-BL features a bespoke steadying system that has been designed to withstand the additional forces that are generated during the milling of straight flutes. Specially developed ‘finger clamps’ ensure the workpiece is held securely while a flute is being milled, then release to enable automatic rotation and positioning ready for milling of the next flute.
Two machines in one
“In what has been a genuine ‘from the ground up’ development of a completely new kind of machining centre, in the 4EX-R-BL we have designed a model that is able to produce all helixes from horizontal to vertical, for helical rotors, infinitive lead blowers, helical blowers, compressor rotors and vacuum pumps. This significant level of versatility makes the 4EX-R-BL well suited to manufacturers who perhaps make different rotor types and therefore need considerable flexibility in their machining technologies, as well as providing a new, highly superior manufacturing solution for producers of Roots-type blowers.”
The Holroyd 4EX-R-BL, at-a-glance:
Workpiece
• Maximum workpiece diameter: Rotor 450mm / Blower 320mm
• Minimum workpiece diameter: Rotor 100mm / Blower 100mm
• Maximum component weight: 900kg
• Maximum (overall) component length (incl. chuck): 1820mm
• Maximum work traverse: 1600mm
Cutter head
• Equipped for cutting with Tungsten Carbide and HSS tooling systems
• Maximum cutter width: Rotor 160mm / Blower 320mm
• Cutter arbor interface: HSK160
• Cutter speed (infinitely variable, unidirectional): 20 – 250 rpm
• Maximum torque at cutter spindle @ 105 rpm: 600Nm
• Maximum Head Angle: +90 / - 55°
CNC control
• Fanuc 31i-series 4-axis CNC system with Macro ‘B’ programming
PTG. The first name in precision
Incorporating the brands of Holroyd, Holroyd Precision Rotors, Binns & Berry and Crawford Swift, PTG has established itself at the forefront of high precision machine tool design, build and supply. The PTG range includes ultra precision grinding machines for rotor, thread and gear operations; rotor milling machines; heavy duty lathes; deep hole boring machines; friction stir welding machines and special purpose machine tools for the manufacture of precision components. Industrial sectors served range from aerospace, medical and mould tool & die to marine, power generation, mining, oil & gas, steel, high end and heavy automotive.
www.holroyd.com