PTG Holroyd reveals new large capacity helical profile grinding machine
Posted by on 11 Jun 2024
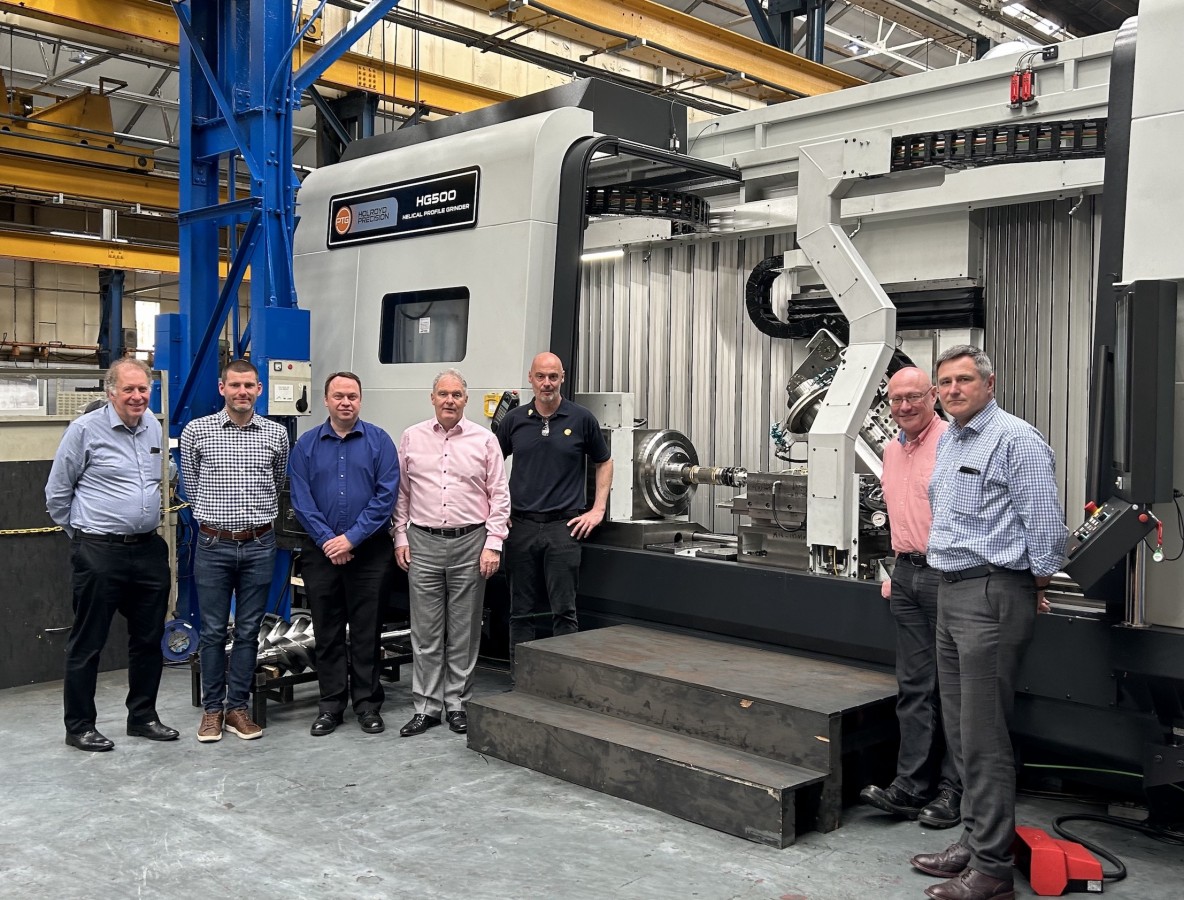
A quarterly regional meeting of The Advanced Machinery & Productivity Institute (AMPI) provided the perfect opportunity for a sneak preview of PTG Holroyd’s soon-to-be-launched, large-capacity HG500 ultra-high-performance helical profile grinding machine.
Held at PTG Holroyd’s Rochdale-based machine tool technology centre on 21st May, the AMPI event included networking opportunities and an update on the institute’s flagship industry and academic-led projects which support manufacturers in the development of world-class machine tool technologies.
After lunch, and with AMPI business concluded, more than 30 delegates commenced a tour of PTG Holroyd’s production facilities – the highlight being a demonstration of the company’s new HG500 helical rotor CNC grinding machine.
“Following the recent, highly successful launch of our smaller HG350 gear grinding centre - the first UK machine tool to use Siemens SINUMERIK ONE future-proof CNC - we realised that a very real need also existed for a new large-capacity helical rotor grinding machine,” says PTG Holroyd’s Engineering Director, Paul Hinchliffe.
“As you can imagine, however, the challenges involved in developing two new machine tools in close succession are considerable, particularly for a UK-based manufacturer operating in the vastly competitive global sector,” he adds. “We were therefore delighted that after reviewing the impressive environmental credentials and performance capabilities of our proposed new HG500 model, AMPI agreed to help support us during the development stages of the machine. As a result, we will be able to launch the HG500 much sooner than would have otherwise been possible. As proud founder members of AMPI - an organisation focused on helping UK companies address their machinery manufacturing challenges - we are grateful for the assistance we have received and are committed to supporting British machine tool manufacturing wherever we can.”
Full details of PTG Holroyd’s new HG500 ultra-high-performance CNC helical profile grinding machine will be available when the machine is officially launched later this year. Utilising Siemens SINUMERIK ONE CNC system, integrated with the Holroyd Profile Management System (HPMS), the HG500 will accommodate workpieces of up to 500 mm in diameter and up to 1,500 kg in weight. Rapid setup of same component batches will be provided via the machine’s data and program files. Operating with two diamond dressing disks, the CNC-controlled dressing unit will provide automatic wheel profile calculation for each dress cycle along with programmable dressing feed rates for roughing and finishing cycles. While in-cycle profile measurement and correction will be delivered using Renishaw’s high-speed, high-accuracy OMP60 scanning probe with SprintTM technology.
“Choosing the SINUMERIK ONE CNC has brought significant user benefits to our HG500 machine, including class-leading integrated safety and failsafe features, enhanced reporting of machine health and performance data, and uncompromising levels of encrypted security,” continues Paul Hinchliffe. “Added to that, it has also allowed us to equip the HG500 with Siemens ‘Create MyVirtual Machine’ and ‘Run MyVirtual Machine’ software capabilities. Used in tandem with our own internal machine design packages, these features have enabled our teams to build virtual ‘digital twin’ HG500 machines on the desktop, then grind virtual rotors – all while observing entire manufacturing cycles, and testing safety and failsafe capabilities. The software also makes acceptance testing exceptionally straightforward, as our customers will be able to sign off on their new HG500 machine before it has even been built. Then, following installation, they will be able to carry out ‘virtual’ helical grinding cycles to ensure right-first-time results.”
Incorporating the brands of PTG Holroyd, PTG Powerstir Friction Stir Welding and Holroyd Precision Rotors, PTG has established itself at the forefront of high-precision machine tool design, build and supply for specialised applications. The range includes advanced machine tools for the production of complex helical components such as compressor rotors, pump screws and high-accuracy gears, and Powerstir machine tools for friction stir welding advanced alloys used in transport applications. With production facilities in the UK, USA and China, Holroyd Precision Rotors manufactures the special purpose, ultra-precision helical components used in a wide range of industries, including refrigeration, air-conditioning, gas and vacuum pumping, industrial air handling, aerospace, medical equipment, motion control, power transmission, power generation, oil & gas, fluid transfer and high-end automotive. PTG also provides advanced technical consulting services.
An initiative led by the National Physical Laboratory and funded through the UKRI Strength in Places Fund, AMPI is focused on helping UK companies address their machinery manufacturing challenges. AMPI’s academic and local authority partners include the University of Manchester, the University of Huddersfield, the University of Leeds, the University of Salford and Rochdale Development Agency. AMPI’s industrial partners include PTG Holroyd, Wayland Additive, Fives Landis Ltd, CR Solutions and Holdson.